Dive into a world where water isn’t just a drink, but a crucial component of the manufacturing process. From quenching thirst to cooling machinery, water plays a vital role in shaping the products we use every day.
But what exactly do manufacturers use water for, and how does it impact their processes?
In this article, we’ll take a deep dive into the nitty-gritty details of water usage in manufacturing, covering everything from the basics of how it’s used, to the benefits, challenges, and best practices for efficiency and sustainability.
So, grab a glass of water (or any other beverage of your choice), get comfortable, and let’s explore the role of water in manufacturing, where every drop counts.
We’ll also be exploring the challenges faced by manufacturers when trying to reduce water usage and waste.
Despite the numerous benefits that come with implementing water conservation practices, there are several challenges involved in making significant changes to water usage. We’ll examine these challenges in detail and discuss ways to overcome them.
Moreover, we’ll be sharing the best practices for improving efficiency and sustainability with water usage.
As a leading provider of water filtration and wastewater treatment technology,
Join us as we dive deep into the role of water in manufacturing and explore ways to conserve this precious resource for a sustainable future.
The Basics of What Manufacturers Use Water For
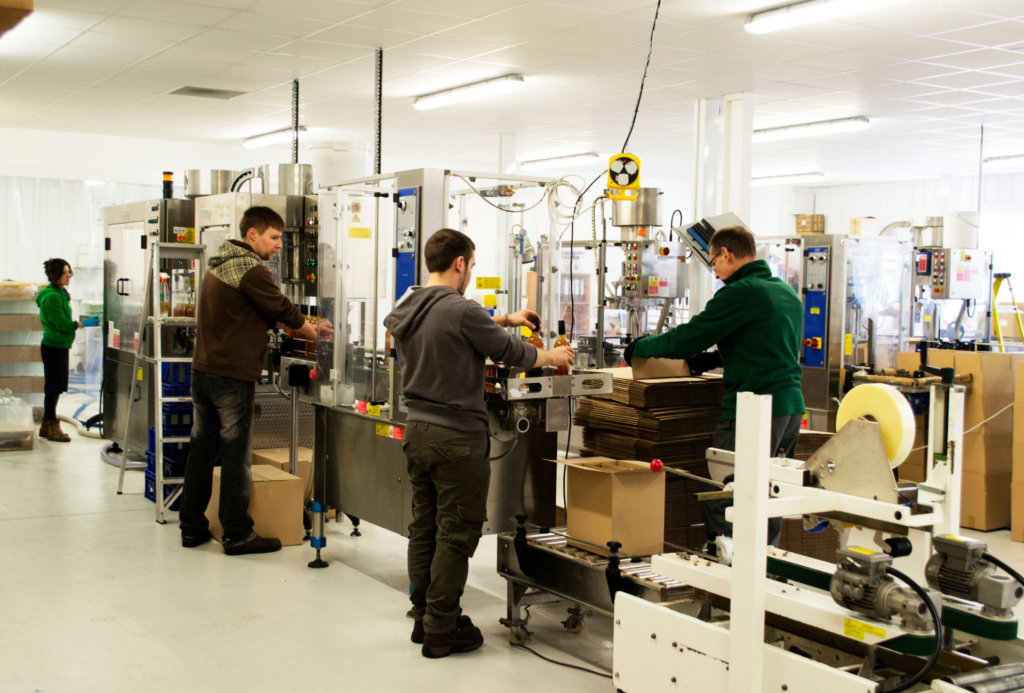
The use of water in manufacturing is essential to the overall efficiency and sustainability of the manufacturing process. From cooling hot machinery to processing raw materials, water plays a crucial role in many aspects of manufacturing.
Water is used in a variety of ways in the manufacturing process. For example, it is used to cool hot machinery and other equipment during manufacturing processes to prevent damage and increase efficiency.
Water is also used as a raw material in certain manufacturing processes, such as in the production of certain chemicals and pharmaceuticals.
In addition, water is an essential part of the cleaning process in manufacturing, as it is used to wash equipment and surfaces to remove dirt, debris, and other contaminants.
In order to conserve this valuable resource, many manufacturers are taking steps to reduce their water usage and improve the efficiency of their operations. This can include using alternative cooling methods, such as air cooling, and implementing water-saving technologies, such as low-flow fixtures and water recycling systems.
By reducing their water usage, manufacturers can help to conserve this valuable resource, reducing the impact of manufacturing on the environment and reducing costs associated with water treatment and disposal.
How Water is Used in Different Types of Manufacturing
Water plays a crucial role in many different types of manufacturing processes.
From the production of chemicals and pharmaceuticals to the manufacturing of consumer goods and electronics, water is used in a variety of ways to support the production process. In this article, we will explore how water is used in different types of manufacturing.
One of the most common uses of water in manufacturing is for cooling purposes.
In many industrial processes, machinery, and equipment generate heat and need to be cooled in order to function properly.
Water is often used to transfer heat away from hot machinery, preventing damage and increasing efficiency. This is especially common in industries such as petrochemical production, where high temperatures are a part of the production process.
Another use of water in manufacturing is as a raw material. In the production of certain chemicals and pharmaceuticals, water is used as a key ingredient in the production process. For example, water is used in the production of hydrogen and oxygen, two key components of many chemical processes.
Additionally, water is used in the production of some consumer goods, such as paper and textiles, where it is used to process raw materials and create the finished product.
Finally, water is also used in the cleaning process in many industries. For example, water is used to wash equipment, surfaces, and finished products to remove dirt, debris, and other contaminants. This is essential for maintaining the quality of finished products and for preventing the spread of contamination in the manufacturing environment.
The Benefits That Come With Implementing Water Conservation Practices
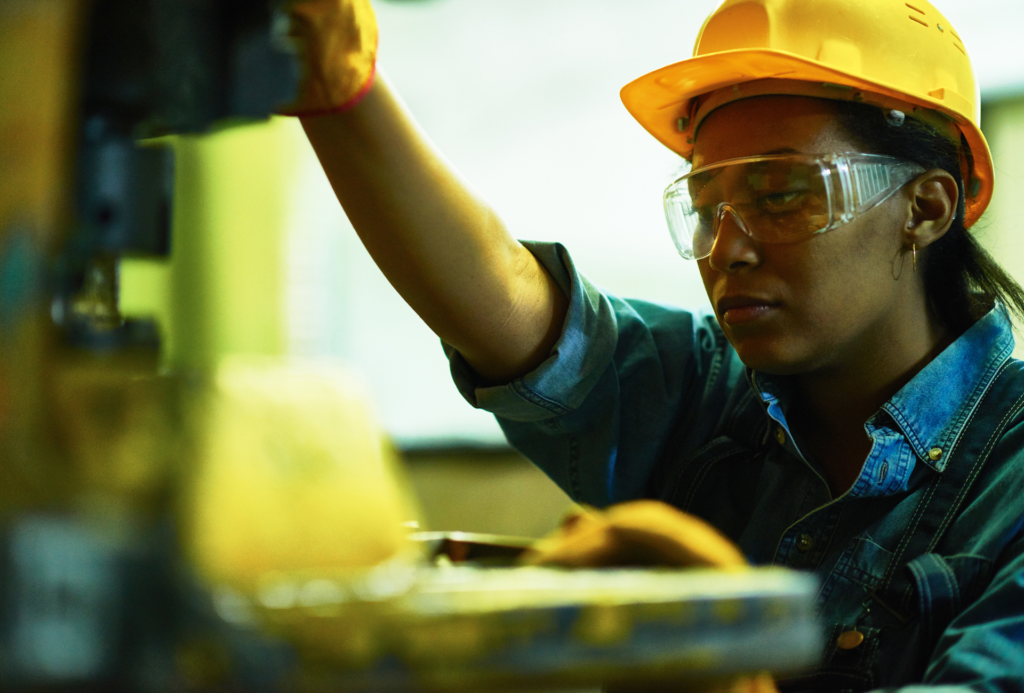
Implementing industrial water conservation methods can bring numerous benefits to manufacturers. One of the most significant benefits is reducing the amount of freshwater required for manufacturing processes.
This can result in substantial cost savings on water bills and the associated wastewater treatment costs. Additionally, reducing water usage can also result in reduced energy costs, as less water requires less energy to pump, heat, and treat.
Another benefit of industrial water conservation is the potential for industrial wastewater reuse. Wastewater generated during manufacturing processes can be treated and reused for other purposes. This reduces the need for freshwater, conserves resources, and helps to reduce the amount of wastewater that needs to be treated and disposed of.
In addition to cost savings and resource conservation, using recycled water for manufacturing processes can also have environmental benefits. By reducing the demand for freshwater, water conservation can help to reduce the strain on local water sources and minimize the impact of manufacturing on the surrounding environment.
To summarize, here are the benefits of implementing water conservation practices in manufacturing:
Pros
- Cost savings on water bills and associated wastewater treatment costs
- Reduced energy costs
- Resource conservation
- Reduced strain on local water sources
- Reduced environmental impact
However, there are also some potential challenges to implementing water conservation practices in manufacturing, such as the cost and complexity of installing and maintaining water treatment and reuse systems.
Nonetheless, the benefits of water conservation for manufacturers and the environment make it a worthwhile endeavor.
The Challenges Faced When Trying to Reduce Water Usage and Waste
While implementing water conservation practices in manufacturing can bring significant benefits, it is not without its challenges. One of the most pressing challenges is preventing industrial waste pollution from factories.
As the demand for water increases, so does the amount of industrial wastewater generated by manufacturing processes. If not treated properly, this wastewater can cause environmental damage and harm to local communities. Reducing industrial wastewater discharge limits and ensuring proper treatment of wastewater can help mitigate this challenge.
Another challenge faced by manufacturers is reducing the environmental impact of their factories. This involves a comprehensive approach that encompasses all aspects of the manufacturing process, from energy usage to waste management.
By adopting sustainable practices and implementing technologies that reduce water usage and waste, manufacturers can reduce their environmental footprint and contribute to a more sustainable future.
The cost and complexity of installing and maintaining water treatment and reuse systems can also be a significant challenge for manufacturers. While the benefits of water conservation are clear, the upfront investment required to implement sustainable water usage practices can be daunting.
However, there are numerous resources available to help manufacturers navigate these challenges and make the transition to sustainable water usage.
Some resources that individuals can use to tackle the challenges of reducing water usage and waste in manufacturing include:
- The US EPA’s Industrial Water Pollution Prevention Program
- The United Nations Industrial Development Organization’s (UNIDO) Industrial Resource Efficiency program
- The World Bank’s Water Global Practice program
- The Alliance for Water Efficiency’s Industrial Water Conservation program
- The American Water Works Association’s Industrial Water Use Efficiency program
By leveraging these resources and implementing sustainable water usage practices, manufacturers can reduce their environmental impact and contribute to a more sustainable future for all.
Best Practices for Improving Efficiency and Sustainability with Water Usage
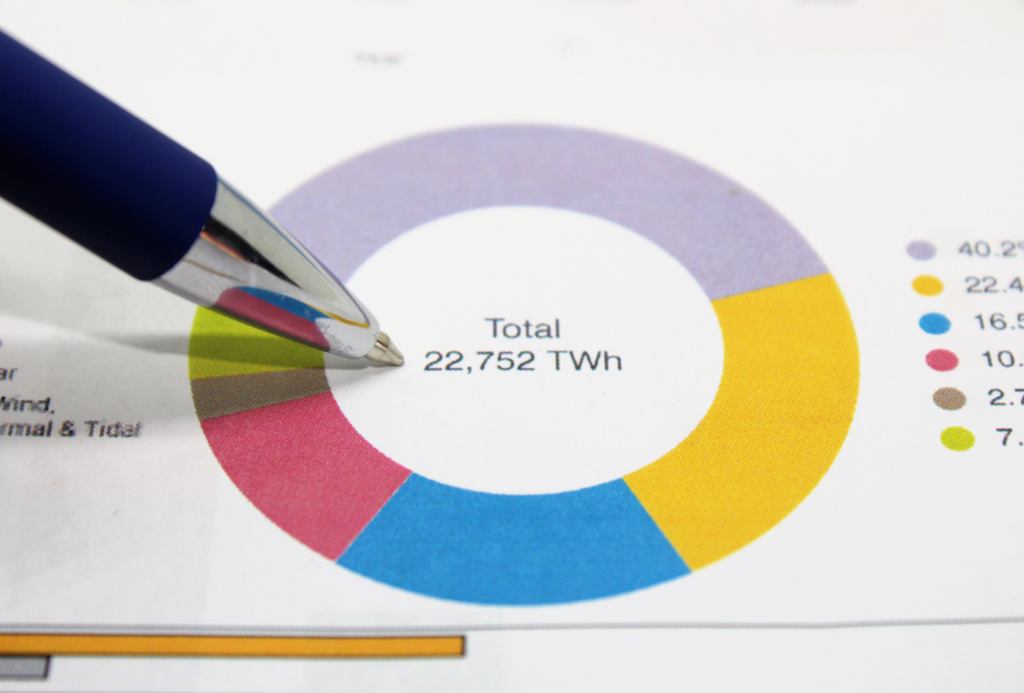
To improve efficiency and sustainability with water usage, it is essential for manufacturers to understand what they use water for in their manufacturing processes. Water is used for a wide range of purposes in manufacturing, including cleaning, cooling, heating, and processing.
By identifying areas where water is being used inefficiently, manufacturers can implement targeted water conservation measures and reduce their water usage.
One best practice for improving efficiency and sustainability with water usage is to conduct a water audit. A water audit can help manufacturers identify areas where water is being wasted and prioritize conservation measures.
This can involve measuring water usage, identifying leaks, and assessing the efficiency of water treatment and reuse systems.
Another best practice is to implement water-efficient technologies and practices. This can include upgrading equipment to more water-efficient models, implementing automated controls to optimize water usage, and using recycled water for non-potable purposes.
By adopting water-efficient technologies and practices, manufacturers can reduce their water usage and associated costs while contributing to a more sustainable future.
Education and training are also essential for improving efficiency and sustainability with water usage in manufacturing. By educating employees on the importance of water conservation and providing training on best practices, manufacturers can promote a culture of water conservation and improve the effectiveness of water conservation measures.
To summarize, here are the best practices for improving efficiency and sustainability with water usage in manufacturing:
- Conduct a water audit to identify areas where water is being wasted
- Implement water-efficient technologies and practices
- Use recycled water for non-potable purposes
- Educate employees on the importance of water conservation and provide training on best practices
By adopting these best practices and implementing sustainable water usage practices, manufacturers can reduce their environmental impact and contribute to a more sustainable future for all.